Eric, ton truc, le Lean
ça ne sert à rien !
Quel beau compliment !

Je vous rassure de suite …
Je ne suis pas masochiste !!!
Croyez-moi, je sais bien faire la différence entre une critique et un compliment …
Mais nous le savons tous. Il est parfois des compliments qui ont un goût amer … et des critiques un goût “sucré”.
Le projet Lean
C’était il y a quelques années, lors d’une intervention au sein d’un atelier de mécanosoudure d’un beau site de production.
L’objet de ma mission était d’accompagner l’équipe en place pour faire évoluer cet atelier d’une production en lots et files d’attente à une production en flux, qui soit tiré par son client, la ligne d’assemblage.
Nous avons fait une Cartographie du flux (VSM) qui, après un gros travail avec toutes les parties prenantes, a abouti à un nouveau schéma d’implantation.
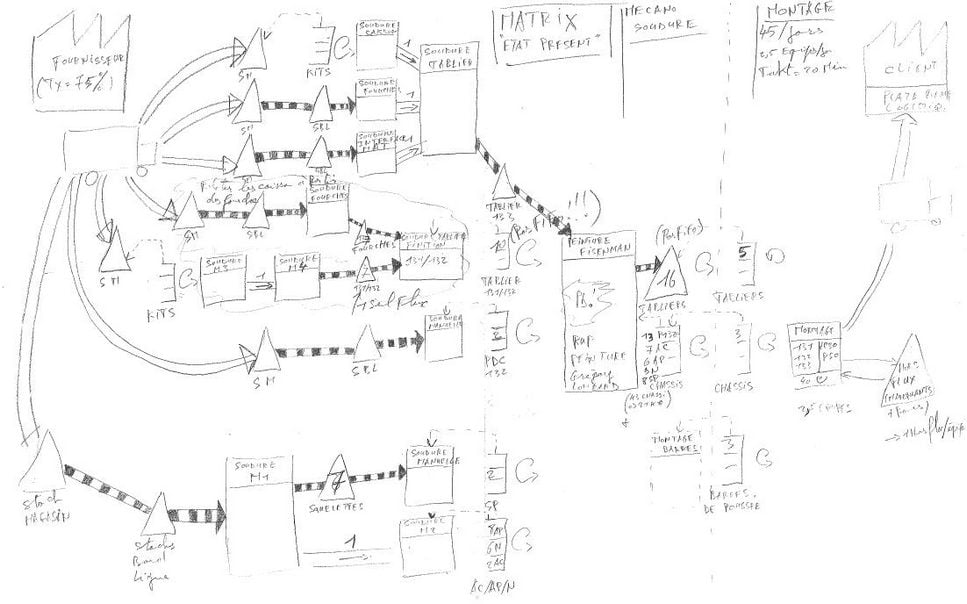
Je ne rentrerai pas davantage dans le détail de l’opération, mais elle a nécessité plusieurs mois de préparations.
L’idée était de modifier l’implantation de l’atelier durant la période de fermeture estivale, afin de pouvoir roder la nouvelle organisation à la rentrée.
Début septembre, nous avons donc passé trois à quatre semaines à accompagner les équipes de l’atelier soudure. À l’issue de ces quelques semaines (grande nouveauté pour les ouvriers et leur encadrement), le volume de production était stabilisé et revenu à la “normale”.
Et la ligne d’assemblage était servie correctement … OUF ! 😊
La voix de l'atelier !
Après cette période de montée en puissance et de stabilisation, le responsable amélioration continue et moi-même, avons décidé d’aller faire un petit sondage (le check du PDCA) auprès des soudeurs. Nous leur avons demandé :
Après un mois de travail dans ce nouvel atelier, avec cette nouvelle implantation et avec cette nouvelle organisation, quel est votre sentiment ? Qu’en pensez-vous ?
Les gars nous connaissant, nous nous attendions à des retours honnêtes et francs. Ce fut le cas. Globalement, pour le vivre tous les jours, ils percevaient les avantages de la nouvelle implantation. Bien sûr, il y avait quelques critiques, notamment sur le fonctionnement d’une équipe à l’autre.
Mais en général, une “satisfaction mesurée” était de mise…
Pourtant, subitement un des soudeurs vint me voir et me dit :
Eric, ton truc, le Lean, c’est bien beau,
mais ça sert à rien !!!
Un peu surpris par sa remarque, ne sachant pas trop “si c’était du lard ou du cochon”, je me suis demandé s’il ne me “chambrait” pas un peu.
Mais non, il était très sérieux …
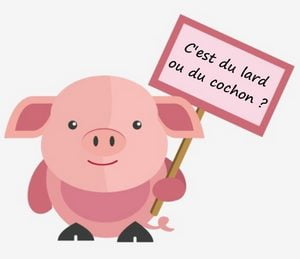
J’engage alors la conversation et lui demande alors pourquoi il me dit ça.
Il n’attendait que cela … et me répond fièrement.
La preuve que ça sert à rien, …
je travaille moins qu’avant !!!
Un beau compliment
Je pense qu’il n’a jamais soupçonné le plaisir qu’il me faisait…
… et cela reste un des plus beaux
compliments professionnels que l’on m’ait fait !!!
J’ai éclaté de rire et lui ai expliqué que s’il travaillait moins tout en sortant la même production qu’avant … alors il pourrait sortir plus en travaillant autant qu’avant.
Après un court instant d’hésitation, tout le monde a rigolé … et lui le premier ! 🙂
Que retenir de cette anecdote?
L’important n’est pas tant le fait qu’ils pensaient tous que le Lean allait les obliger à travailler plus vite dans les mêmes conditions de travail.
Non, c’est aspect là, nous l’avions anticipé en travaillant avec eux sur le terrain, en montrant les plans, en “prêchant la bonne parole”, en expliquant, expliquant, expliquant, … ce que nous faisions.
Mais certaines croyances ont la vie dure… et certains syndicats ne sont pas étrangers à ce fait … 😉
Non, l’important est …
… qu’ils confondaient travail et Valeur Ajoutée !
En fait, leur quotidien était “ponctué” par énormément de gestes, de mouvements et de déplacements qui n’apportaient aucune valeur ajoutée.
Par exemple :
- déplacer plusieurs fois des pièces parce qu’on ne sait pas où les poser et qu’elles gênent
- faire des déplacements inutiles pour poser ou prendre des accessoires, car aucun support n’est prévu au poste (voir la méthode 5S)
- “bidouiller” de loooongues minutes avec le palan électrique et les élingues, car la potence de celui-ci est trop courte
- s’emmerder à contourner 100 fois par jour un container vide que la logistique n’a pas évacué
- etc., etc., etc.
Nota : Rien que le fait d’écrire ces quelques exemples, cela me met dans une colère noire ! Sans être donneur de leçon, je me demande …
Comment peut-on à ce point manquer de respect aux opérateurs ?
Or, la nouvelle organisation / implantation avait justement diminué un peu de ces non valeurs ajoutées.
Cette anecdote a au moins eu le mérite de faire prendre conscience aux gars que leur travail était en permanence “pollué” par du gaspillage, du Muda.