Quel était leur besoin ?
L’entreprise ne parvenait pas à répondre à la demande client sur une de ses principales gammes de produits
Ils ne produisaient pas assez de chariots par jour et souhaitaient faire un bon de productivité conséquent
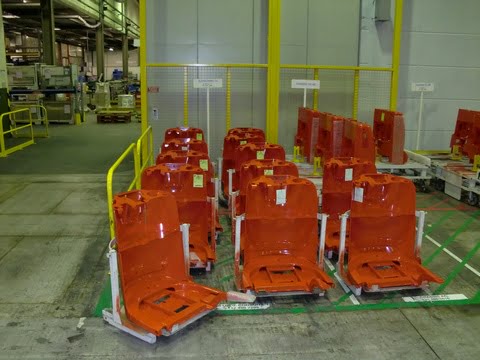
qui débordent et d'autres en quasi-rupture
Quel était le problème ?
Nous avons constaté trois problèmes majeurs :
- La ligne d'assemblage était en rupture de châssis (éléments maitres)
- Lorsque des châssis étaient disponibles, les parties fixes et mobiles ne correspondaient pas
- Enfin, il arrivait que la paire châssis fixe/châssis mobile soit présente, mais pas dans la bonne référence
De ce fait, la ligne d’assemblage subissait de nombreux arrêts tout au long de la journée, pénalisant notablement sa performance.
Notre démarche
Nous avons utilisé l’outil VSM afin de visualiser et d’analyser le flux de fabrication dans sa globalité. L’état actuel de la VSM a montré :
- Un découplage entre le flux aval (ligne d'assemblage) et son flux amont
- Le flux amont fonctionnait en flux poussé, générait de la surproduction et ne répondait pas correctement à son client (la ligne)
L’état cible de la VSM a abouti à :
- La mise en œuvre d'un vrai flux tiré par la ligne d'assemblage
- Une réorganisation et réimplantation du flux amont
- L'accrochage des châssis en peinture par paire de (fixe+mobile)

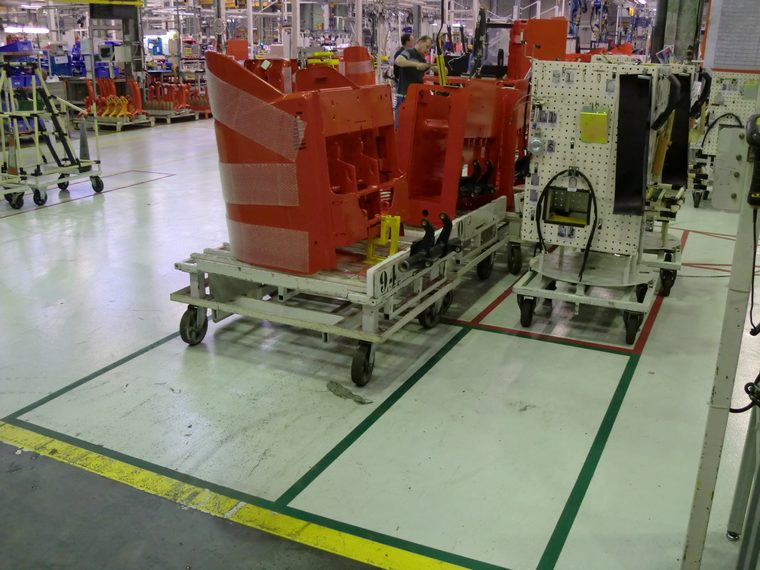
Chiffres & Résultats
Productivité
45 à 60 chariots/jour (+ 33 %)
Bilan financier après 18 mois
Durée du projet : 9 mois
Coût global du projet : 180 k€
Gain global sur la période : 380 k€
Retour sur Invest. (ROI) : 8,6 mois